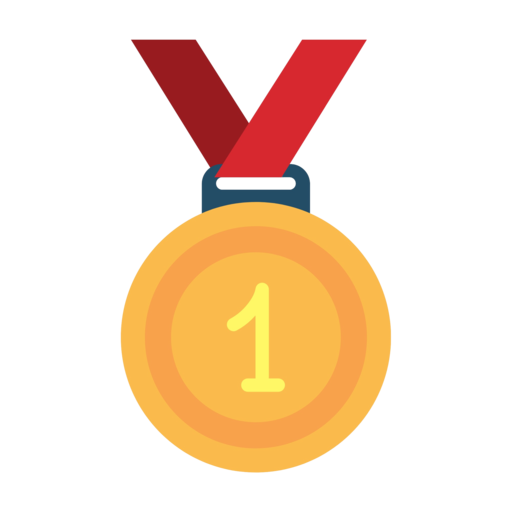
Reddit mentions of ANNIMOS 20KG Digital Servo High Torque Full Metal Gear Waterproof for RC Model DIY, DS3218MG,Control Angle 270°
Sentiment score: 3
Reddit mentions: 4
We found 4 Reddit mentions of ANNIMOS 20KG Digital Servo High Torque Full Metal Gear Waterproof for RC Model DIY, DS3218MG,Control Angle 270°. Here are the top ones.
- ▶Upgraded Version - advanced linearity and accuracy with precision potentiometers,stable,low noise,water-proof
- ▶Large Torque - maximum torque is up to 21.5 kg/cm (298.5 oz/in)@6.8V
- ▶High Quality - equipped with strong copper & aluminum gears,CNC aluminium middle Shell
- ▶High Rotation - well-controlled, 270 degree rotation. 360 degree rotation when power-off, perfect for robot joint activities
- ▶Dimensions - 1.58x0.79x1.60inch (40x20x40.5mm);Weight: 60g (2.12oz) only
Features:
Specs:
Color | Red |
Height | 0.79 Inches |
Length | 1.58 Inches |
Width | 1.6 Inches |
▼ More
#1 of 47
I run these Annimos servos and they are great and are super cheap. This one has twice the torque of the spektrum one
https://www.amazon.com/dp/B076CNKQX4/ref=cm_sw_r_cp_api_i_wFoUDbWRP70K1
Credit goes to my wife and her friend for the decoration. That was all faux fur from JoAnn's Fabric and acrylic paint. I did the frame and robot stuff :) I had to do a lot of work on the joints because they did not bend. I wanted it lower to the ground so the tail did not have to be so long and to give it a better look and more stability.
Dog skeleton (on sale right now for 10 bucks!):
https://www.homedepot.com/p/Home-Accents-Holiday-3-ft-Animated-Skeleton-Greyhound-with-LED-Illuminated-Eyes-6342-36559/206770838
Servos:
https://www.amazon.com/gp/product/B076CNKQX4/ref=ppx_yo_dt_b_asin_title_o01_s01?ie=UTF8&psc=1
Hardware:
Raspberry Pi 3 B+
Servo control: Adafruit 16-Channel PWM / Servo HAT (https://www.adafruit.com/product/2327)
UI: Adafruit OLED Bonnet (https://www.adafruit.com/product/3531)
I was able to stack both the servo control board and OLED Bonnet on the Pi. I love this OLED Bonnet because it has a joystick and buttons so it provides a mini UI. I wrote a menu program for the Bonnet that loads on boot and lets me start the program for the tail and do an orderly shutdown.
Yep, so far only 1 out of 12 has failed. That was due to a high speed.impact. so far waterproof,. ANNIMOS 20KG Digital Servo High Torque Full Metal Gear Waterproof for RC Model DIY, DS3218MG,Control Angle 270°
Great work!
I do agree, that the 'multi arm' approach is the way to go (EDIT: triple arm minimum, as I just did some testing and with only two arms there is really no way to effectively stabilize 'anything' that you are holding as the item tends to easily rotate out of control), unless you have access to a 3d printer and effectively free filament, etc.
The geared linear approach was done as a 'cheapest' first attempt to duplicate TempestVR's and tomotomox's work in linking a robot directly to VAM. After having done that, and then done the tcp/ip connection, I moved directly now to the multiple servo/axis approach. It is funny how much less printing will be required, lol.
Also, in ref to the geared linear approach, I was working on modifying the gear for the 20kg amazon servo I had bought DS3218MG ( https://www.amazon.com/ANNIMOS-Digital-Waterproof-DS3218MG-Control/dp/B076CNKQX4) as seen here ( https://imgur.com/a/OMaqHPL ), and per the dimensions in the images for the servo, the arm has a stated furthest hole of 23.5mm, turns out I had to do a few prints of test gears as the hole was actually at 24.5mm! Not to mention, where the central 'hub' is, it is different from the MG995R, so, that then now threw off the 'gearing' being properly mated and so then there is play between the rack and pinion, lol! With a multiple servo/axis setup, that wouldn't be an issue at all! The only alignment issues are effectively those due to the proper synchronized control of the 2+ servos.
I looked into using the ram mount too, and like it, but I think I'm going to go with this https://www.amazon.com/VIVO-Monitor-Adjustable-Articulating-STAND-V001/dp/B00B21TLQU/ , it is meant for holding up 22 pound monitors, so I think it shouldn't oscillate too much while the robot is in motion. In addition it can be mounted to a desk, to the side of a bed, and has a nice long articulating arm and 75 and 100mm VESA mounts which will be easy to 3d print something to attach to. A non-clamped version that you could 'sit around' is here https://www.amazon.com/VIVO-Computer-Free-Standing-Adjustable-STAND-V001H/dp/B01FE2BCR8/
So at this point, I'm currently printing the housing for the new multi axis robot for testing, it will be a 3-4 servo setup in the end, might have a few variants. Going to be using an adafruit servo hat https://www.amazon.com/2327-Raspberry-Servo-Development-Board/dp/B00SI1SPHS/ and a raspberry pi and the tcp/ip VAM connection.
Lastly, once I get the multiple axis setup, I will then move to the code/algorithms such that there can be a seemless transition from the VAM 'movements' to the new robot(s) based on it's features. The idea is to make all this as seemless and easy as possible for anyone to do themselves.
And all thanks to TempestVR for all his contributions, without him I wouldn't have done any of this!